How to build a circular economy
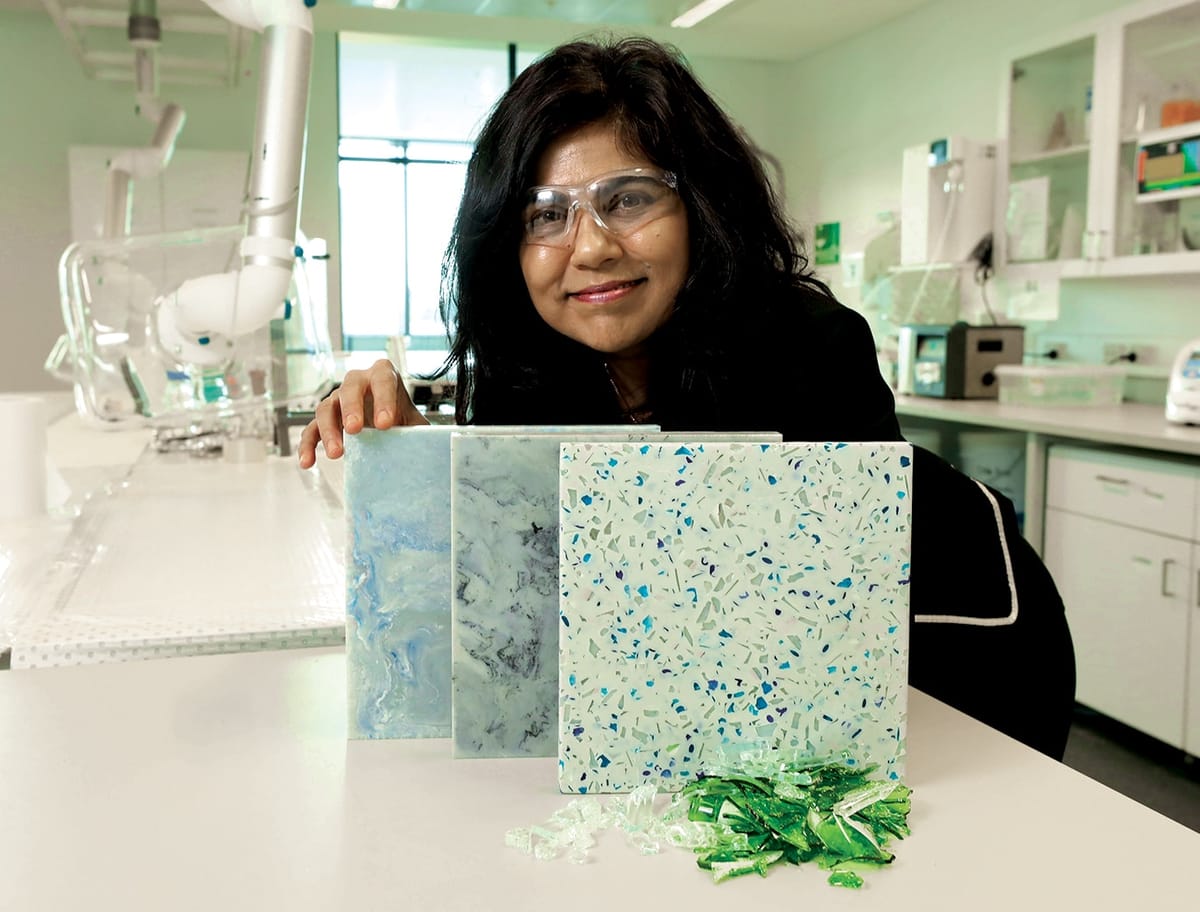
by Professor Veena Sahajwalla /
Highlighting an innovative Nowra recycling project in this op-ed feature, engineer and inventor, Professor Veena Sahajwalla, explains how MICROfactories extract commercial value from waste materials and point the way to sustainability.
At a waste depot in Shoalhaven, NSW, 200 km south of Sydney, old mattresses, fabric and dirty glass left over from household recycling are being transformed into something completely different: Green Ceramics, a versatile commercial product.
These high-performance, nontoxic hybrids can be used for a variety of architectural and decorative applications, including furniture and ceramic tiles. The materials that go into them are difficult to recycle using traditional methods, which means they usually end up in landfills. But now they have a new purpose.
The Shoalhaven Green Ceramics Microfactorie, which went online in October last year, is among the first of its kind. It was developed through a partnership between the local city council, Kandui Technologies and UNSW’s Sustainable Materials and Technology (SMaRT) Centre, a research centre aimed at translating new recycling science into real-world environmental and economic benefits. The partnership has been supported by UNSW, EPA Trust, OCSE, and recently the Trailblazer for Recycling and Clean Energy.
This Microfactorie can process around 450 tonnes of glass, mattresses and other textiles per year, but it is part of a much bigger concept – the movement towards a ‘circular economy’, which would get rid of the ‘throw-away’, consumer economy that relies on continuous extraction and use of raw materials and production of huge amounts of waste.
Instead, production and consumption are aimed at minimising resource extraction, cutting down waste and lowering carbon emissions. Sustainability in every step in the cycle is the goal.
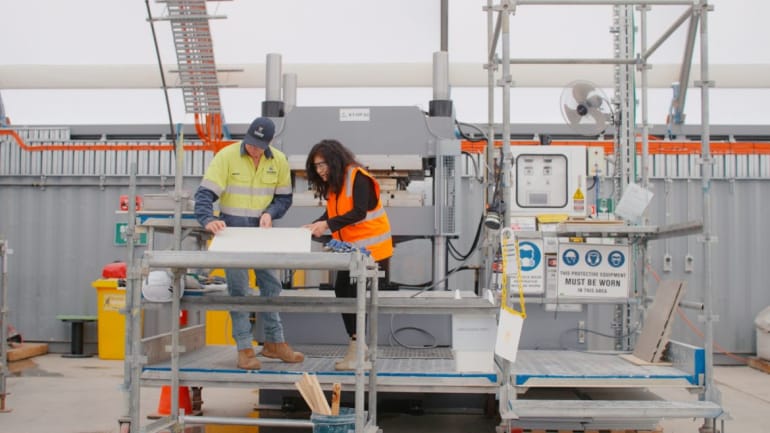
The circular economy idea is growing in parallel with environmental movements and awareness of climate change. Processes around extracting raw materials, product manufacturing and waste disposal are carbon intensive and rely on finite resources.
Along the way, as conservation and sustainability have evolved into mainstream concerns, people and communities have adapted to different ways of dealing with waste. Recycling has become a routine for most people – many local government councils in Australia have programmes for recycling paper, plastic and glass, and recycling clothing, electronics and other materials has become more commonplace and more accessible.
The ‘reduce, reuse, recycle’ mantra is familiar to everyone, but the circular economy is about more than that – one key element that makes it different from business-as-usual is ‘reform’.
Reforming is about reimagining, redesigning and remanufacturing – not taking old bottles and turning them into new ones, but taking old plastics and turning them into new plastic filaments to be used in a 3-D printer to make all kinds of new objects, or taking old bottles and mixing them with old textiles and turning them into new Green Ceramics.
With technology, the equation is more complex. The vast amounts of e-waste produced by obsolete, outworn and discarded technology present huge challenges. Many of the devices that people depend on every day contain rare earth metals that are costly and in short supply. They frequently contain a variety of other valuable metals. And they are constructed with high-grade polymers.
Given the way technology products – mobile phones, computer hard drives, circuit boards, battery packs and so many others – are designed, constructed, and integrated, taking them apart can be an extremely difficult puzzle. So, they often end up in landfills, creating environmental hazards, or they are shipped off to places where poverty and desperation create economies of extraction, pulling apart the remnants of technology to salvage any valuable materials and discarding the rest.
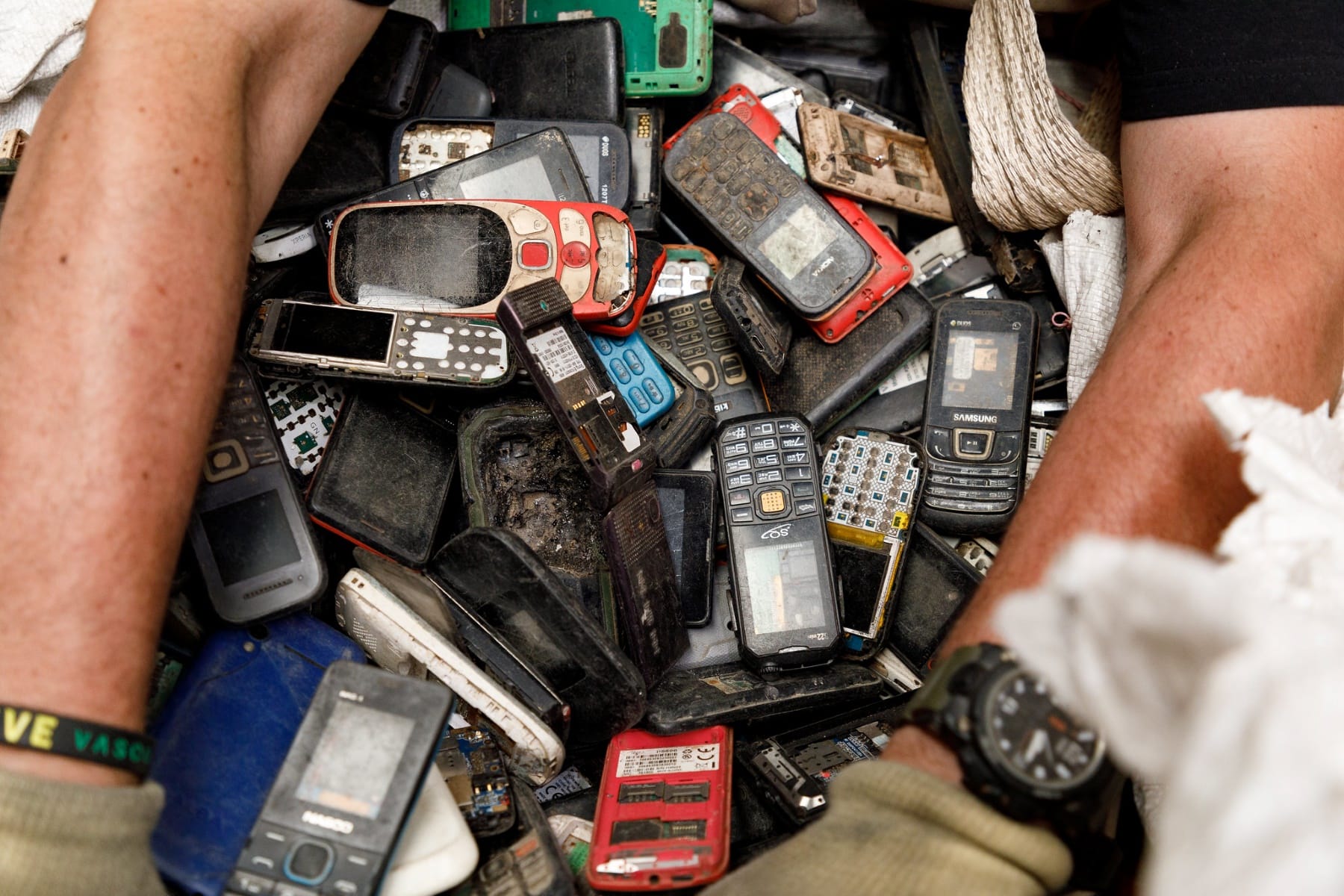
But new methods developed by the SMaRT Centre have created ways to deal with these challenges. The Microfactorie concept is central to the process – using the right tools, techniques and mechanisms to disassemble complex e-waste and recover the materials that went into it.
Microfactories are designed to be either co-located to the waste source, such as a landfill, or located with an end-user, such as a manufacturer, to enable the substitution of virgin resources with waste materials.
Their adaptability – the ability to perform the right tasks for the given inputs, and to create usable outputs based on need – creates economies of purpose. Each of the modules may look very different in each region, creating products and tackling waste in a way that is relevant and useful to the communities and industries they are a part of.
Through successful embodiments of the circular economy, everyone will begin to view waste as a valuable resource. But it will take everyone in the value chain collaborating to redesign and remanufacture products to reduce the pressures on our planet and create more sustainable communities.
A few years ago, no one would have imagined that a partnership between the local council, a university research centre and an industrial enterprise could lay the foundation for remanufacturing in the region with products made from waste glass and textiles being installed in new commercial and residential developments across the country.
What is happening on a landfill site in Shoalhaven is proof that, with imagination and commitment, the circular economy is within reach.
Professor Veena Sahajwalla is Founding Director of the UNSW Sustainable Materials Research and Technology (SMaRT) Centre and an Australian Research Council Laureate. She is an internationally recognised materials scientist, engineer and inventor. In 2018, Veena launched the world’s first e-waste MICROfactorie and in 2019 she launched her plastics and Green Ceramics MICROfactories. She was named the 2022 NSW Australian of the Year in recognition of her work.
Anirban Ghose, head of Microfactories at the Smart Centre at UNSW, contributed to reporting.
Originally published under Creative Commons by 360info™.